机械电焊臂,借助 AI 和 CV 检测缺陷
机械电焊臂是工厂的重负荷机器,在最极端的环境中焊接钢铁。这些机器尽管十分坚硬,仍无法检查工作质量,即使在出现常见错误如孔隙时,也无法识别。在焊接过程中如果没有法线这些缺陷,那么可能需要破坏性、成本高昂的重新工作,或需要裁掉部分材料。
传统质量控制包括调用高级焊接技术人员,使用视觉和声响指标来检测孔隙。但这些专家检测的实际效果有限。组装线上焊接的钢铁有几英里,不可能光靠视觉检查出每一个孔隙。而且没有辐射和超振动技术,他们无法看到焊接面的底部。因此,焊接成品出了工厂之后,很可能成为报修产品。
幸运的是,创新技术能够提供解决方案。AI 驱动的焊接机器可以提高质量控制水平,为制造商提供绝对优势。
视觉缺陷检测能够捕捉缺陷
农业设备制造商 John Deere 是一个很典型的例子。这家公司使用气态金属弧来焊接构建机械器具所需的高强度钢。全球 52 家工厂中,数百台机械臂每年使用数百万磅焊接电线。
有这样大的生产量,公司必须寻找在焊接过程中识别缺陷的新方法。公司找到了 ADLINK,一家边缘计算解决方案全球制造商。
ADLINK 的 AI 和计算机视觉为 Edge 电弧焊接缺陷检测解决方案提供支持,使 Deere 能够实时观看焊接池,以便在问题发生时及时发现和改正。
“机器学习让 John Deere 更好地了解了每次焊接的质量,” ADLINK 边缘解决方案高级总监 Daniel Collins说。“从保修和传递信息的角度来看,这些功能都非常强大实用。”
硬件 + 预装软件
弧焊平台包括软件和硬件,基于使用英特尔® 酷睿™ 处理器和英特尔® Movidius™ Myriad™ X VPU 的工业级机械视觉平台。
MeltTools 焊接摄像头(专用于高温高亮度环境下)—安装在了机械臂上,距离焊接处仅 12 到 14 英寸。预训练的机器学习模型使用集成 ADLINK 边缘物联网软件,可以捕捉、直播、处理、理解视觉数据并采取行动。ADLINK 架构允许制造商在边缘插入模块软件和硬件,以创建连续数据流程(图 1)。
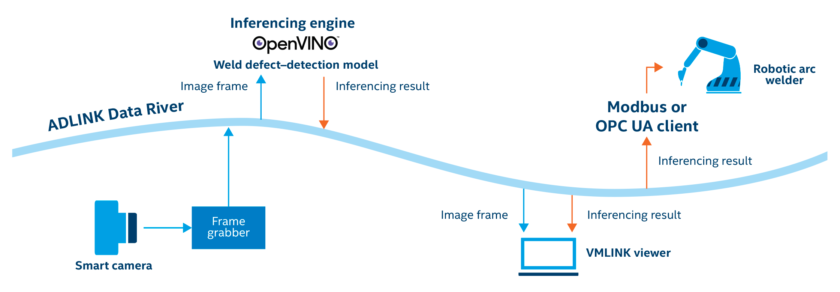
“该软件是平台能够顺利运作的一大重点”,Collins说。“它包含英特尔® OpenVINO™ 工具套件推理引擎—一个机器视觉计算器,以及 ADLINK Edge — 它拆分成了几个应用程序。这些应用程序能够处理摄像头数据,上传至推理引擎,解读结果,并采取行动。这些都使用 ADLINK Data River 或边缘通信层实时进行。”
一个决策应用程序将等待引擎的推理结果来评估焊接质量。如果其要求停止焊接,一个 DIO 程序将向机器人发起 24 伏的信号,暂停电焊。同时,还会向工厂车间经理发送警报说明电焊已停止。
“如果在一个批次完成后才发现质量问题,他们很可能要查看该批次中所有焊接点来进一步检查和操作。这可能意味着完全拆除,从头开始。”Collins 说。
AI 为系统集成商 (SI) 带来商机
机械电焊商业空间不断增长,大型制造商逐渐弃用手动电焊,为系统集成商创造了巨大的机会。
Collins 说,“从机械电焊质量检测的方面来看,您会发现在焊接工作中没有多少要检查的东西,”“但您会看到各种组件,如摄像头和模型等。您看不到组装在一起的单个产品中的所有组件或部件。”
ADLINK 套件专为 PoC 设计,包括机器视觉算法,大约可以识别电焊中常见的 10 个质量检测问题中其中 1 种。要为客户定制解决方案,SIs 可能需要进行某些配置或重新训练模型。
Collins 表示,“新环境中的客户可能能够利用不寻常的解决方案识别孔隙,同样的,我们也需要进行一些模型再培训累增加在该环境下的准确性。我们完成了正确识别所有组件需要做的必要基础工作。SI 的任务是进行配置,让他们的客户在部署后能够立即获得其价值。”
Collins 补充道,此外许多制造商还对“焊接质量检验即服务”感兴趣。“我们可能有机会提供托管服务,”他说。“这与不断增长中的行业相结合,加上为每位客户的环境进行配置和重训,SI 将创造客观的服务营收。”
计算机视觉和机器学习将机械电焊臂变成工厂的超英雄,能够发现本来会被忽略的缺陷。利用 AI 技术,制造商和提供服务的 SI 在当今的竞争市场中获得了优势。